|
Post by PinkFloyd on Sept 24, 2010 22:01:35 GMT
NO NO NO! First off measure the voltage across each 1K5 resistor (at the points shown).... there is one per channel..... adjust each 500R trimpot VR4 / VR5 to get as close to 1.2V as you can. 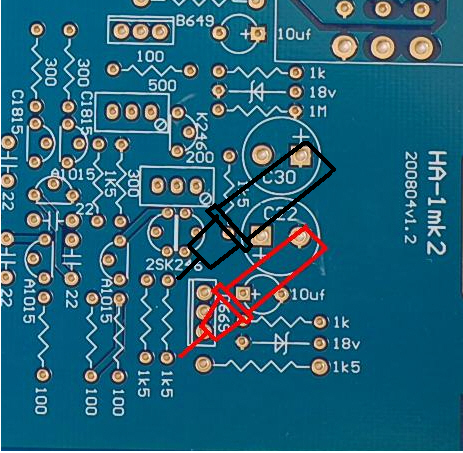 OK.... now measure the DC offset at the headphone socket.... probe between tip and sleeve and ring and sleeve (sleeve being the ground) www.rock-grotto.co.uk/dcoffset.htmMake sure your meter (if it is not autoranging) is set to the millivolt setting "mV" NOT the Volts setting.... also make sure it's the DC setting. You say you measured 200mV DC (0.2V) , that is way too much...... Measure, as per www.rock-grotto.co.uk/dcoffset.htm and tweak the 200R trimpots VR2 / VR3 (one per channel) until you get the DC offset below 10mV per channel. Once you get the DC offset down I think she will work fine  Mike. OK now the voltage over the 1500 is 1204 mV and 1205 mV, the offset is between 0 and -1 mV.. No sound, it also does not click when i turn it on anymore ?? The 200 trimpots does not seem to work the offset is the same when I turn the pot ?? The 200mV must have been a mistake because it showed zero as I messured it again..  Check all your solder joints thoroughly then.
|
|
|
Post by PinkFloyd on Sept 24, 2010 22:10:46 GMT
No more I can say Claus, sorry, fault finding is now up to you...... clue, the parts are likely to be 100% ok.... it's most probably a soldering error somewhere on the board.
Mike.
|
|
|
Post by meliphicent on Sept 25, 2010 1:16:40 GMT
:S Reading other peoples problems makes me realise this isn't going to be as simple as "paint by numbers". I'm still triple excited though - I am enjoying my current amp and apparently this one poops on it from a great height so I can't wait!
|
|
leo
Been here a while!
Team wtf is it?
Posts: 3,638
|
Post by leo on Sept 25, 2010 8:06:28 GMT
Its hard fault finding this sort of thing without having it infront of you. Did you take any close up pics ?
|
|
Deleted
Deleted Member
Posts: 0
|
Post by Deleted on Sept 25, 2010 8:19:35 GMT
:S Reading other peoples problems makes me realise this isn't going to be as simple as "paint by numbers". I'm still triple excited though - I am enjoying my current amp and apparently this one poops on it from a great height so I can't wait! Guys here make it look easy but my own past experience has also been the fact that it's not hard to get the parts in the right place, it's the after-care ... the board has no diagnosis programme to let you know what has gone wrong so you end up looking for one or even more problems. Knowledge helps to try and diagnose but dry/touching joints etc can be so difficult to spot. I decided long ago, you're often better off trusting the guys who know and pay more for it!!! It's also because I really haven't got the patience for the job. I built a synthesiser a long time ago and still remember the pain and the anger and the frustration. When I see Mike's work, (and Frans too) it's absolutely clean and meticulous. I haven't got the patience for that. (I know my limitations!!) I also think that people who produce stuff like that are rare nowadays, unless it was made by a machine.  However, I admire Claus getting in there. I'm sure you'll get it in the end Claus. Trouble is, it can be something so tiny.
|
|
Deleted
Deleted Member
Posts: 0
|
Post by Deleted on Sept 25, 2010 8:30:16 GMT
Its hard fault finding this sort of thing without having it infront of you. Did you take any close up pics ? Claus They should be high res photos to help identify any suspect solder joints etc. Being able to see the actual colour codes on resistors can also be of assistance in comparing with the schematic or layout diagram. Alex
|
|
Deleted
Deleted Member
Posts: 0
|
Post by Deleted on Sept 25, 2010 9:22:11 GMT
@ Claus
Will see if I can make time on sunday to G-mail chat and attempt 'remote repair' if you have not been able to fix it by then.
|
|
Deleted
Deleted Member
Posts: 0
|
Post by Deleted on Sept 25, 2010 9:25:41 GMT
I have just ordered some of the solder recommended by Mike, as i find the all silver solder difficult to work with, hope to have it delivered by Tuesday and will have a go at populating the board on Wednesday. Is it advisable to use soldering flux on each joint when using this solder Mike, i have always used it on the lead solder when soldering a joint, if all goes well should have all the components installed by end of next week, and a close up photo posted, so any obvious errors can be spotted by you professionals out there.  Mick.
|
|
Deleted
Deleted Member
Posts: 0
|
Post by Deleted on Sept 25, 2010 9:39:59 GMT
Mick High quality solder as used in general electronics work should not need flux.. Flux is normally built in to the solder, which usually has a resin based core.Many fluxes are actually corrosive, and should not be used with normally avaiable electronics type solder. Occasionally flux may be used to help soldering if the joint to be soldered is tarnished due to age. Normally, this is a last resort. We needed to use flux on occasion with older telephone exchange piano wire connections, when cleaning with a brass bristle brush (also a last resort) was not effective. Alex
|
|
|
Post by PinkFloyd on Sept 25, 2010 10:01:00 GMT
I have just ordered some of the solder recommended by Mike, as i find the all silver solder difficult to work with, hope to have it delivered by Tuesday and will have a go at populating the board on Wednesday. Is it advisable to use soldering flux on each joint when using this solder Mike, i have always used it on the lead solder when soldering a joint, if all goes well should have all the components installed by end of next week, and a close up photo posted, so any obvious errors can be spotted by you professionals out there.  Mick. Hi Mick, No, don't use flux.... just use the solder. Mike.
|
|
|
Post by clausdk on Sept 25, 2010 11:29:04 GMT
@ Claus Will see if I can make time on sunday to G-mail chat and attempt 'remote repair' if you have not been able to fix it by then. Thanks Frans I inspected the joints yesterday and I reheated some, but I also did connect two joints that should not have been joined I think), I have tried sucking and using solderwick, but they won't come apart  I hope you will have bigger succes with yours Lars.. However if it all fails, I have another Panda on the way  If a first you do not succeed, try again  I also looked at a new solderstation on fleabay but there are so many, what is recommended ?? I want a decent quality, fast heatup is also on the wishlist and of course a high VFM..
|
|
|
Post by PinkFloyd on Sept 25, 2010 12:29:42 GMT
Pictures of these joints please Claus!
|
|
Deleted
Deleted Member
Posts: 0
|
Post by Deleted on Sept 25, 2010 16:07:06 GMT
hi Mike i know it's a big ask but if you could give Claus some key voltages to measure as it may make finding the fault a bit faster. not all voltages but just the most important ones.  this may show up miss-placed or faulty components and dry joints. if the relay is not switching anymore but still no sound then that may be faulty? could be good to check the psu voltage to it (is it 12v i'm not sure but just a thought). Claus some photo's of the board top and bottom would be great. it's going to work i can feel it in my bones  take care
|
|
|
Post by clausdk on Sept 25, 2010 19:01:11 GMT
|
|
|
Post by PinkFloyd on Sept 25, 2010 19:50:46 GMT
The fact it was working for 2 minutes, then stopped, then worked again and now is not working at all would suggest to me that something is causing an intermittent short. Looking at all the schrapnel on the board it is possible that a piece of stray solder is touching something it shouldn't touch. Get yourself a hard toothbrush and some isopropyl alcohol (tape head cleaner) and scrub the board until all of these deposits are removed.... see how you get on with that 
|
|
|
Post by PinkFloyd on Sept 25, 2010 20:02:24 GMT
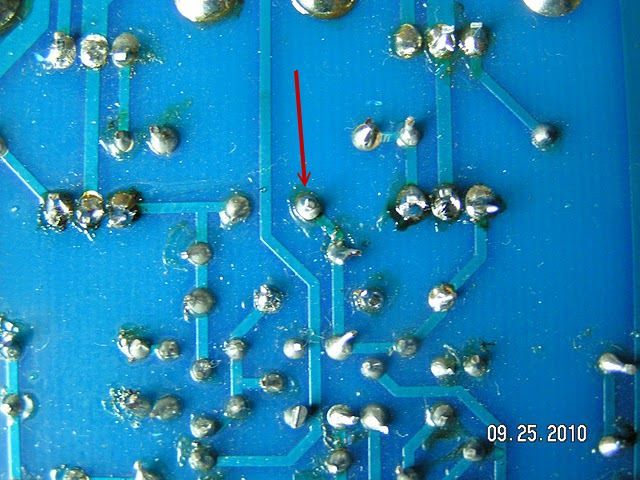 Is it just a shadow or has this pad become detached from the track? Do a continuity check between joints.... ie the meter will peep when the continuity is ok, if it doesn't peep there is a break. If that pad "has" parted company with the track then scrape the track surface until copper is exposed underneath, solder onto that copper.... or just get a piece of wire and solder from pad to pad to make the connection. I'm pretty certain it's either an intermittent short cause by a rogue piece of solder on the board OR one of the pads has parted company with the track.... check everything carefully AFTER you have cleaned the board. Mike.
|
|
|
Post by PinkFloyd on Sept 25, 2010 20:55:47 GMT
|
|
|
Post by PinkFloyd on Sept 25, 2010 21:14:32 GMT
Looking at your two "kissing joints"....... they are both on the ground plane so it doesn't matter as they are already kissing each other under the surface  Do you have a desolder pump Claus? They only cost a couple of quid.... personally, I would desolder a few of those joints and see what's going down underneath all those molten lumps  When you resolder the joints be sure to use a hot iron (400C +) and make sure you constantly clean the tip on a damp sponge.... apply the iron to the joint and then feed the solder in.... allow it to form a "pool" and then withdraw the soldering iron tip. You should NOT have blobs of solder all over the board, this shows you haven't got the soldering technique quite correct yet. If your iron is too cold it will barely melt the solder and you will end up with jagged "peaks" instead of nice smooth joints.... these through hole plated board rely on some solder flowing through to the other side. It is essential that you use a GOOD low melting point "leaded" solder". The more I look at the board the more I am absolutely certain that this is either a dry joint, an intermittent short or a lifted pad. Tale your time, go over every joint with a magnifying glass and do a continuity check on any suspect joints. Mike.
|
|
Deleted
Deleted Member
Posts: 0
|
Post by Deleted on Sept 25, 2010 21:33:13 GMT
Well i have all the resistors and diodes in the board awaiting soldering, all parts accounted for with no spare resistors or diodes left over. Looking good so far ;D Mick. PS Mike, what are the two small blue ones(look like resistors) that go in the two 1M positions on the board, are they resistors!!!!!!. 
|
|
|
Post by PinkFloyd on Sept 25, 2010 21:54:04 GMT
Well i have all the resistors and diodes in the board awaiting soldering, all parts accounted for with no spare resistors or diodes left over. Looking good so far ;D Mick. You will find the "future" solder VERY nice to work with Mick  450C is a nice temperature to work with, in and out / job done..... just watch the solder and as soon as it "pools" on the joint then pull out the iron. So..... solder tip on the pad / leg of component.... keep it there for a second or two and THEN feed the solder into the joint.... we are initially heating both the pad and the legs of the part and then flowing in solder to join both in holy matrimony..... no point in flooding molten solder over a cold pad..... heat the pad / legs up first and then feed the solder in.... ie: push it into the pad until it floods the joint.... THEN remove the iron when you are happy. That solder I recommended is beautiful stuff, it melts like butter and unless you have Parkinson's disease (or St. Vitus Dance) your joints will be perfect and you will not have blobs of solder sprayed all over the place 
|
|
leo
Been here a while!
Team wtf is it?
Posts: 3,638
|
Post by leo on Sept 25, 2010 21:56:14 GMT
Looking at your two "kissing joints"....... they are both on the ground plane so it doesn't matter as they are already kissing each other under the surface  Do you have a desolder pump Claus? They only cost a couple of quid.... personally, I would desolder a few of those joints and see what's going down underneath all those molten lumps  When you resolder the joints be sure to use a hot iron (400C +) and make sure you constantly clean the tip on a damp sponge.... apply the iron to the joint and then feed the solder in.... allow it to form a "pool" and then withdraw the soldering iron tip. You should NOT have blobs of solder all over the board, this shows you haven't got the soldering technique quite correct yet. If your iron is too cold it will barely melt the solder and you will end up with jagged "peaks" instead of nice smooth joints.... these through hole plated board rely on some solder flowing through to the other side. It is essential that you use a GOOD low melting point "leaded" solder". The more I look at the board the more I am absolutely certain that this is either a dry joint, an intermittent short or a lifted pad. Tale your time, go over every joint with a magnifying glass and do a continuity check on any suspect joints. Mike. Very good advice, I'd certainly want to desolder some of those joints especially the ones close together , re do them, cleaning off the thick treacle looking flux with pcb cleaning fluid, it'll probably leave the board feeling a little sticky but at least it'll help show any tiny shorts which may be hidden under the flux. If the tracks/pads are delicate desolder mop may be kinder to the tracks although to be honest the track looks good quality and shouldn't lift
|
|
leo
Been here a while!
Team wtf is it?
Posts: 3,638
|
Post by leo on Sept 25, 2010 22:00:45 GMT
Could also try going over it with a stiff dry nail brush and give it a blow after. Obviously not something with bristles so stiff it makes a mess
|
|
Deleted
Deleted Member
Posts: 0
|
Post by Deleted on Sept 25, 2010 22:15:49 GMT
These any good  On a more helpful note, @ Mick, 1M = 1 mega ohm (1,000,000 ohm) resistor.
|
|
|
Post by PinkFloyd on Sept 25, 2010 22:23:24 GMT
These any good  On a more helpful note, @ Mick, 1M = 1 mega ohm (1,000,000 ohm) resistor. That's just silly Chris.... 
|
|
leo
Been here a while!
Team wtf is it?
Posts: 3,638
|
Post by leo on Sept 25, 2010 22:24:53 GMT
Well i have all the resistors and diodes in the board awaiting soldering, all parts accounted for with no spare resistors or diodes left over. Looking good so far ;D Mick. PS Mike, what are the two small blue ones(look like resistors) that go in the two 1M positions on the board, are they resistors!!!!!!.  I don't have the kit so can't be 100% but I am sure Dale resistors are available in blue , its possible the brown ones don't do a value as high as 1meg so they provided an alternative series of Dale resistor which comes in a different colour. is there a number printed on the body ? something like 105 ?
|
|